Имитационная модель производственной линии на базе сложной конвейерной системы
1. Проект *
Разработка и применение имитационной модели производственной линии для контроля и испытаний коробок перемены передач.
2. Область применения проекта
Область применения и реализации результатов проекта – предприятие машиностроения, выпускающее двигатели и коробки перемены передач для большегрузных автомобилей.
Предприятием, которое заказало проект и которое реализовало его результаты на одном из заводов, является TyssenKrupp EGM GmbH, Лангерхаген, Германия.
3. Научно-техническое описание
Объектом моделирования является производственная линия, на которой выполняются контроль и испытание коробок перемены передач (в дальнейшем – изделий) для дизельных двигателей большой мощности. Основой конфигурации линии является замкнутая конвейерная система, с помощью которой осуществляется транспортировка изделий, установленных на специальных носителях. В форме чертежа общего вида линия показана на рисунке 1, а в форме эквивалентной замкнутой системы массового обслуживания – на рисунке 2. Обработка изделия начинается с его установки на носитель на рабочей станции 1, далее оно перемещается еще через 10 рабочих станций, на последней из которых производится снятие изделия с носителя, что является завершением цикла его обработки. Носитель не покидает конвейерную систему, и после разгрузки на станции 11 он опять поступает на станцию 1, где на него устанавливается новое изделие. На станциях 1-4 и 7-11 операции выполняются рабочими, а на параллельно работающих станциях 5.1-5.8 и 6.1-6.7, где проводятся основные операции по испытанию изделий, режим работы является полностью автоматическим.
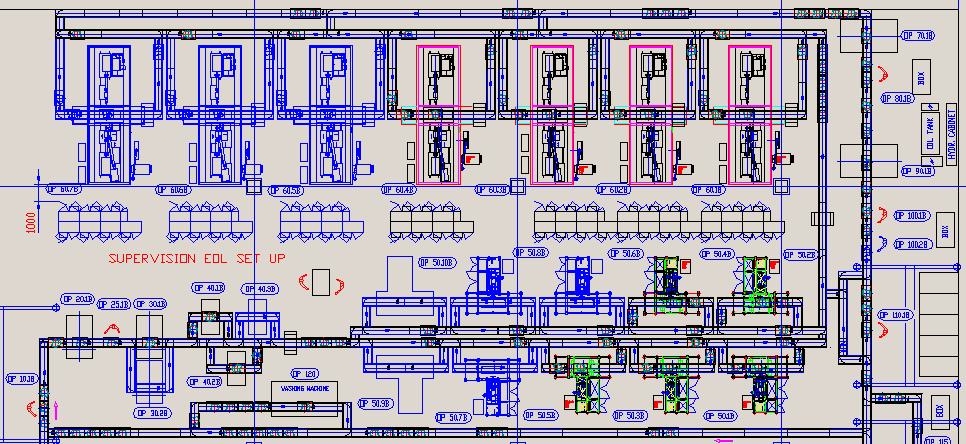
Предполагается, что на вход производственной линии могут поступать изделия четырех типов A, B, C и D партиями размером от 1 до 200 единиц. Этот факт непосредственным образом влияет на реальную производительность автоматических станций 5.1-5.8 и 6.1-6.7, так как возникает необходимость производить их переналадку, связанную с изменением типа обрабатываемых изделий. При повышении частоты выполнения операций по переналадке сокращается возможное полезное время работы станций и, как следствие, их реальная производительность (пропускная способность). Было принято решение, что поиск «удачных» алгоритмов переналадки автоматических станций при различных последовательностях партий изделий проще всего осуществить путем составления соответствующих эмпирических правил, эффективность которых может быть проверена путем прямого имитационного моделирования.
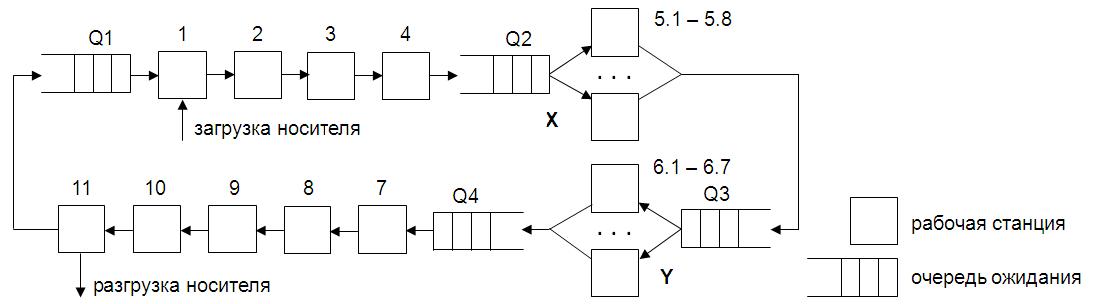
Рисунок 2. Представление производственной линии в виде замкнутой системы массового обслуживания
Имитационная модель производственной линии была разработана с использованием коммерческого пакета имитационного моделирования Plant Simulation (до 2005 года пакет имел название eM-Plant). Основу структуры модели составляют 163 блока типа line, с помощью которых представляются отдельные секции роликового транспортера, отображающие в совокупности полную конфигурацию моделируемой конвейерной системы (рисунок 3). Подвижные объекты модели отображают носители, при этом применяется принцип моделирования «с ориентацией на длину», при котором положение каждого носителя точно отображается на одной или одновременно двух смежных секциях транспортера с учетом длины как носителя (0,7 м), так и соответствующих секций транспортера.
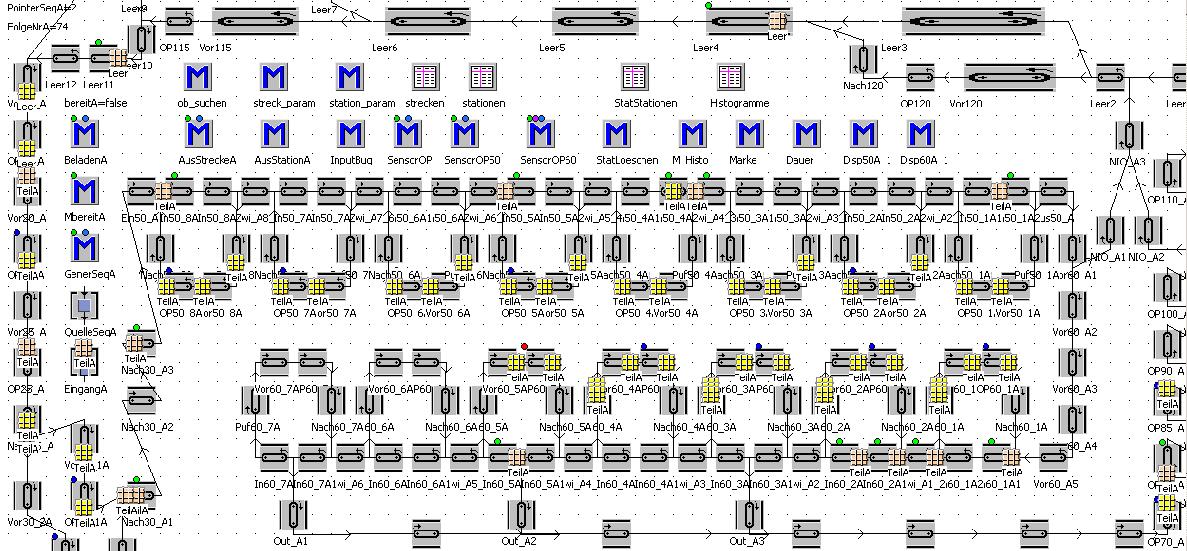
4. Стадия разработки проекта
Проект выполнялся с октября по декабрь 2007 года и является завершённым проектом.
5. Результаты (прогноз результатов) проекта (работы)
Результатом проекта являются оптимальные стратегии переналадки автоматических станций, найденные для заданных типов последовательностей изделий и обеспечивающие максимум пропускной способности системы.
6. Организация, реализующая проект
Университет Отто фон Герике, кафедра Логистических систем, Магдебург, Германия.
Все фазы проекта, включая программирование модели, были выполнены одним экспертом – Толуевым Юрием Ивановичем.
7. Финансирование
Бюджет проекта – 12 тыс. евро. Источник финансирования – средства заказчика, т.е. проект был выполнен на договорной основе.
8. Обзор рынка
Проект выполнялся силами университета в Германии, который ориентируется примерно на 300 евро за один человеко-день работы, т.е. для данного проекта были предусмотрены 40 рабочих дней. Институты Фраунгоферского общества могут заключать договора, в которых стоимость одного человеко-дня достигает 1 тыс. евро. Инженерные бюро, выполняющие работы по имитационному моделированию, ориентирутся на 400-800 евро за один человеко-день.
9. Контактная информация
Адрес электронной почты: juri.tolujew@iff.fraunhofer.de.
10. Литература
Толуев Ю., Змановская Т. Имитационная модель производственной линии на базе сложной конвейерной системы // Автоматизация в промышленности, 2013, №7, с. 37- 41.
* Информация о проекте размещена на сайте www.simulation.su с разрешения разработчика модели – Толуева Юрия Ивановича. Копирование, распространение и переопубликование размещенных материалов или их фрагментов без письменного разрешения разработчика запрещено.